Company Profitability
- Bruce Dodds
- Oct 17, 2024
- 2 min read
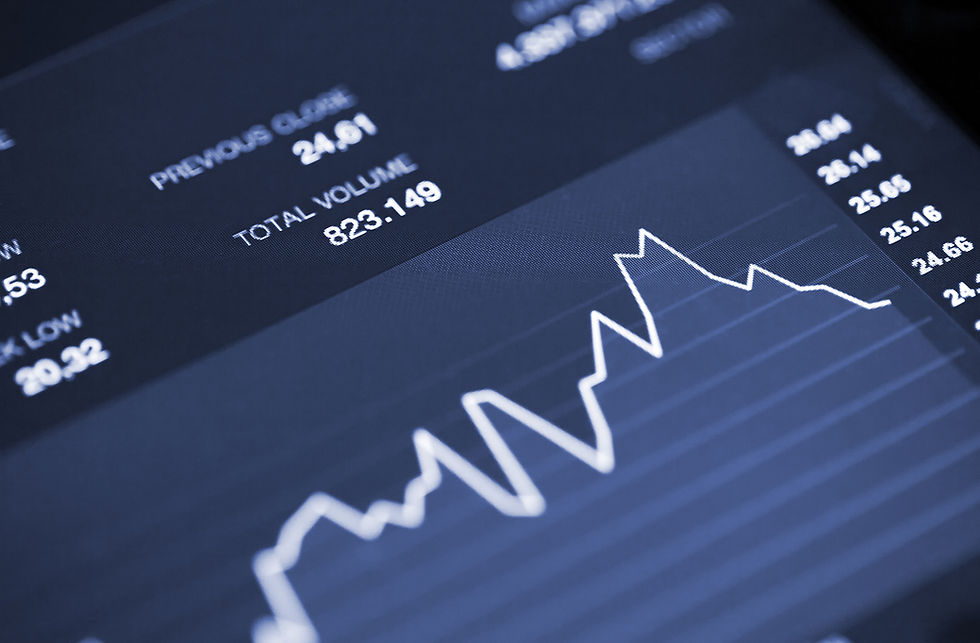
October 2024
MANUFACTURING FACILITY INTERNAL FUNDING OF CAPITAL PROJECTS
Manufacturing facilities exist to serve their Stakeholders by providing quality products, which are consumed internally or are typically sold into the retail market. Successful manufacturing facilities generate revenues in excess of their costs to operate their facility. The incremental revenues are used to ‘grow the business’ by reinvesting in the facility. The revenues are distributed as outlined in the facilities Business Plan. Funds set aside for the facility fall into one of four categories, which are Regulatory, Maintenance, Safety/Environmental and Discretionary. It should be noted that external market conditions (raw material costs, utility costs and labor costs) can impact the cost to produce the products being marketed.
Due to limited capital funding, there is intense competition between the facility departments for each discretionary dollar. Similarly, within the Capital Project slate of projects there is a second level of competition for funding between four distinct types of projects as outlined above. It should be noted that Discretionary projects typically require economics to support any funding request.
THE STORY OF GROWTH
If facilities are to continue to improve their profitability over time, they must continually improve their competitive position year-over-year in their retail market position. Failure to do so will result in reduced income and thereby reduced funding for Capital Projects.
Simply stated, the manner in which Capital projects are executed has a direct correlation to the future of the facility.
How do we compete in a competitive marketplace? We can maintain our competitive advantage by utilizing the Five Pillars of Project Management Execution on every project better than our competitors.
THE CAPITAL PROJECTS GROUP RESPONSIBILITY FOR PROJECT EXECUTION
The goals of the Capital Projects Group were to execute projects using the five pillars of execution with a focus on the following:
Cost effective execution within the approved Budget;
Safely implemented with no Lost Time Incidents;
Deliver a Quality Project to our Customers that they are proud to operate (Operations, Maintenance and Safety);
Schedule is achieved on-time; and,
Project Risks are mitigated throughout project execution.
Failure in any one of these areas will affect the facilities profitability.
THE IDEAL OPERATION VERSUS OUR OPERATION
I quote Jimbo Fisher, the past football coach for Texas A&M, “Every time you touch the football it is for a National Championship.” Likewise, every activity performed during capital project execution should be completed with the goal to improve the facilities profitability.
One of our department goals should be to identify the “Ideal Manufacturing Operation” and then work to “close the gap” between our current position and the Ideal position (refer to Figure 1.1 below). The challenge is that since the Ideal position is constantly improving over time, we must continually improve over time. If we do not choose to improve, we will lose our market position and Customers who buy our products.
Comments